Transforming Supply Chain Operations for a Leading Business Airline
A case study
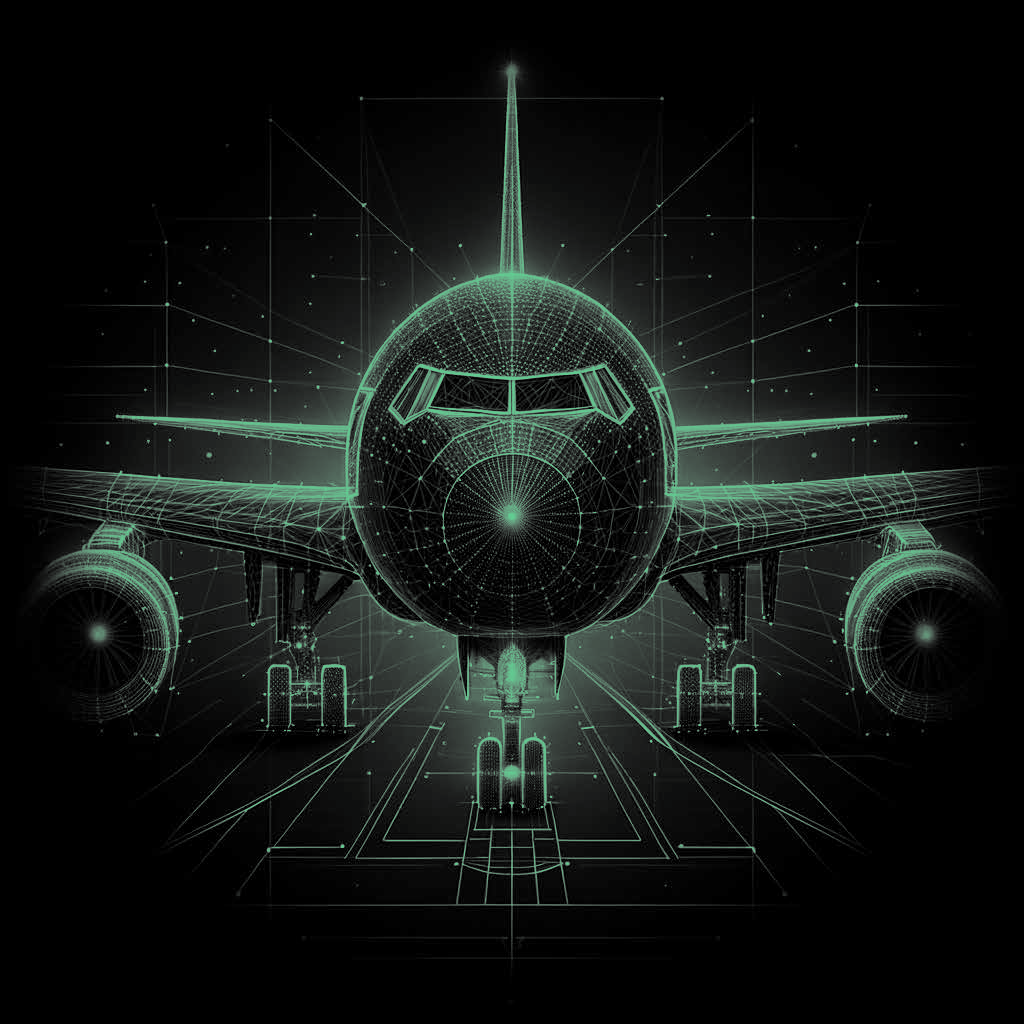
The Challenge
A leading business airline company operating a fleet of 750 aircraft faced significant challenges in managing its spare parts inventory. With a team of 20 dedicated to tracking parts, the company grappled with excessive inventory, frequent AOG (aircraft on ground) events due to missing parts, and substantial losses from damaged or lost shipments.
To address these issues, the airline implemented Sensos' Sync Control Tower, a centralized platform that provided real-time visibility and control over both outbound and inbound shipments. Leveraging Sensos' globally connected labels, the airline gained precise location tracking and automated shipment journeys based on predefined rules.
By utilizing Sensos' advanced features, the airline achieved remarkable results
► Reduced inventory value by 10%: By optimizing stock levels and minimizing excess inventory, the airline significantly reduced its inventory carrying costs.
► Eliminated lost parts: Sensos' real-time tracking prevented parts from being lost or misplaced, resulting in a $1 million annual saving.
► Accelerated part replenishment: Average round trip time for parts was cut in half, minimizing AOG time and improving operational efficiency.
► Reduced operational overhead: Automated processes and data-driven insights streamlined operations, leading to cost savings and increased productivity.
► Enhanced dispute resolution: Sensos' detailed shipment data helped resolve disputes related to damaged shipments efficiently.
By harnessing the power of Sensos, the airline transformed its supply chain operations, achieving significant cost savings, improved efficiency, and enhanced customer satisfaction.
Updated about 2 months ago
Get in Touch. We’re Here to Help.
Let’s discuss how Sensos can transform your logistics operations:
Contact Us